Definitions
2.1 RECOVERY SYSTEM DEFINITIONS
Defining the components and terminology of a parachute recovery system will help to avoid misunderstandings between Government agencies, prime contractors, and sub-contractors.
Although a parachute recovery system is a subsystem or even a subsystem of a prime system, common usage refers to all parachute recovery subsystems and assemblies as systems. Figure 2-1 also shows the typical breakdown structure of a target drone recovery system containing-in addition to the parachute recovery system--sequencing, impact attenuation, flotation, location, retrieval, and docking equipment.

Many parachute recovery systems contain fewer components than are listed in Figure 2-1. For example, an aircraft landing deceleration parachute system consists of a compartment in the aircraft with door actuators and the parachute disconnect mechanism, and, separately within the compartment, a parachute assembly comprising an ejectable pilot chute, pilot-chute bridle, brake parachute, brake-parachute deployment bag, and riser with disconnect clevis.
Figure 2-2 is a schematic of a typical ejection seat parachute assembly with descriptive nomenclature. Many variations of the assembly are possible: independent main-parachute deployment, stabilized high-altitude descent on the drogue chute, seat stabilization by attitude sensors and reaction control system (RCS), velocity-altitude control of the parachute deployment sequence, and man-seat separation. The variations may result in more or fewer components and different component arrangements.
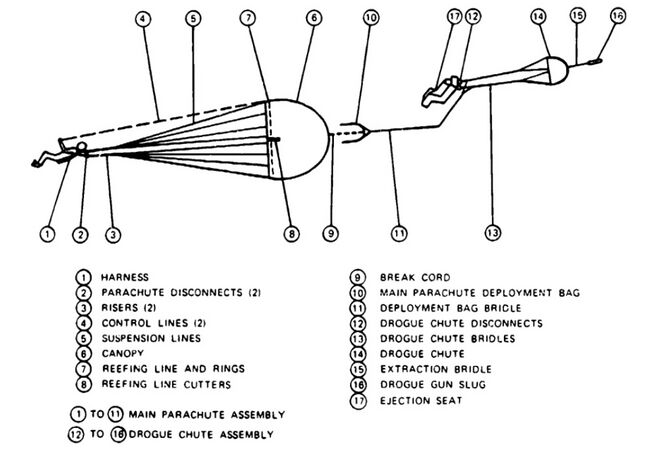
2.2 PARACHUTE RECOVERY SYSTEM APPLICATIONS
The first recorded development and application of parachute-type devices involved the lowering of animals, and occasionally humans, during fairs and carnivals in 14th- and 15th-century Siam and China. Parachute development in Europe and the United States began in the 18th century for use in exhibits and shows. The first application of parachutes for saving the lives of aviators occurred during World War I. Since that time, parachutes have been used for the rescue of aviators; for premeditated jumps of military and civilian personnel; and by sport parachutists, smoke jumpers, and paramedic jumpers.
An airdrop of military personnel and equipment is the final phase of transport to a theater of operation. Personnel and equipment must land uninjured, undamaged, and ready for action or use.
Aircraft in-flight and landing deceleration involves the termination of dangerous flight maneuvers, such as spin, deep stall, and high-speed flutter. In these cases, the parachute is disconnected after the aircraft reaches a controlled flight attitude. Many militaries) and some civilian aircraft use parachutes as landing brakes to shorten the landing roll and save tires and brakes.
Many ordnance devices, such as bombs, mines, torpedoes, and submunitions, are parachute-retarded to let the aircraft escape the effective range of the weapon, to stabilize and retard the weapon before water entry, to obtain antiricochet impact angles, and to obtain a desired splinter-distribution pattern after impact.
Air vehicle recovery includes termination of flight, and recovery for reuse of targets, unmanned vehicle systems, booster rockets, and manned and unmanned spacecraft. Some of these are recovered by the Midair Retrieval System (MARS).
Parachutes are also used to decelerate high-speed land vehicles, rescue speedboat crews, and decelerate ships. Figure 2-3 lists today's primary parachute applications.
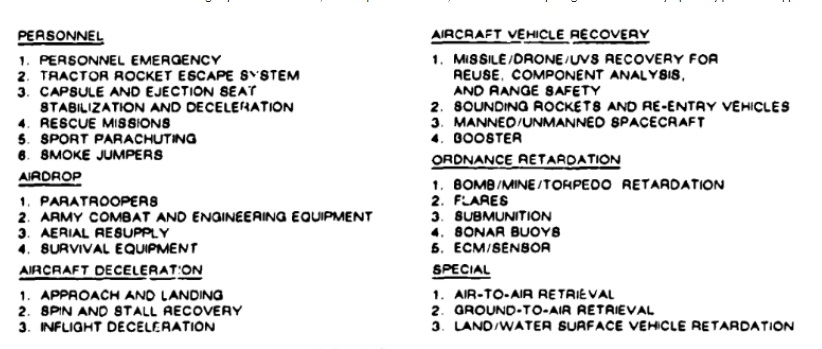
2.3 RECOVERY SYSTEM BOUNDARIES
The application range of parachutes with regard to velocity and altitude was closely associated with the speed and altitude capability of aircraft until the 1950s. A research program conducted in the late 1940s and early 1950s established that parachutes could be used at supersonic speeds; parachutes developed specifically for supersonic application followed. Parachutes have been used successfully at speeds in excess of Mach 4.0, at altitudes up to the limits of the atmosphere, and at dynamic pressures to 15,000 psi. Parachutes have also been used to recover a rocket booster weighing 185,000 pounds. Figure 2.4 gives the required parachute performance envelopes for different applications.
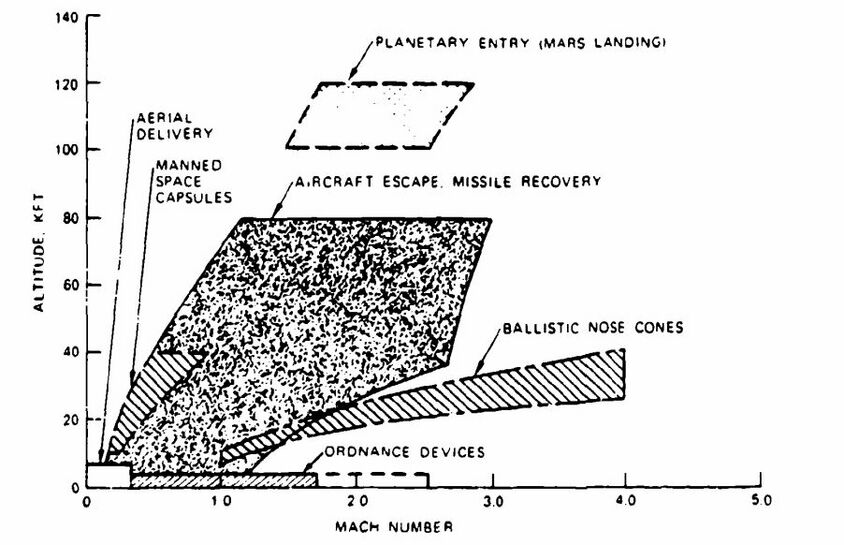
Figure 2-5 shows the approximate velocity and altitude boundaries of parachute systems that are presently in service or have been tested experimentally. Boundary limits are moved upward, and outward as new materials are introduced that shift the aerodynamic heating limit to higher temperatures and make possible the recovery of heavier vehicles. Successful landings on Mars have been made, and vehicle landings by parachute on Venus and Jupiter are in preparation.
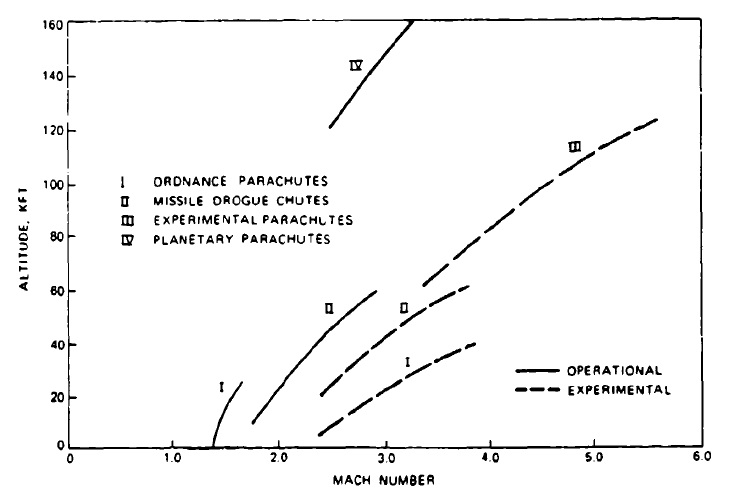
2.4 PARACHUTE RECOVERY SYSTEM DESIGN CRITERIA
Prerequisites for the design of a parachute recovery system are an understanding of the purpose of the system and its requirements, and a clear definition of the design criteria governing system and component selection. Figure 2-6 lists typical design criteria.
System reliability will always be of utmost importance. Parachute recovery systems have reached a high degree of reliability, as documented by the 31 consecutive, successful, manned spacecraft landings and the high reliability rate of paratrooper parachutes. In complex systems, it is mandatory to analyze and review all aspects and components of the total recovery system cycle. Failure to integrate the system totally can lead to the type of mishap experienced by Space Shuttle flight 7 in 1983, when a wrong sensor signal caused premature parachute to disconnect, and the solid-fuel boosters were lost.
Weight and volume are important considerations. Parachute assemblies constitute approximately 5% of total vehicle weight for lightweight vehicles, and 3 to 4% for vehicles weighing several thousand pounds. A complete recovery system. including flotation, location, and retrieval assemblies, will weigh 10 ± 2% of the total vehicle weight. The 560-pound Apollo parachute assembly that was carried around the moon and back to Earth, where it was needed for landing, was a major expense in terms of weight, and much effort was dedicated to eliminating ounces to reduce overall spacecraft weight.
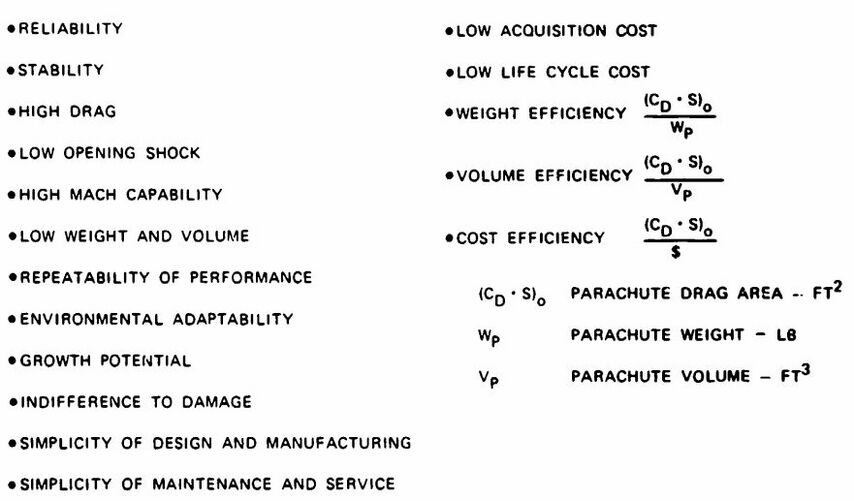
For aerial targets, the recovery system is used only for recovery and retrieval in the last minutes of the mission. Each pound saved in the recovery system will either benefit the performance of the target or permit an increase in payload.
The selection of the parachute frequently begins with the stability requirement. Aircraft deceleration parachutes, first-stage drogue chutes, and most ordnance-retardation parachutes require a high level of stability-a requirement that automatically eliminates many high drag parachutes.
A final descent parachute, the high-weight item in any recovery system, is usually selected from high drag, solid textile parachutes that result in the smallest diameters and, consequently, the lowest weights and volumes. Limited parachute oscillation (0 to 10 degrees) of large final descent parachutes may be acceptable or may be eliminated by use of cluster parachutes.
A high drag coefficient is important in selecting the final descent parachutes. However, a better evaluation criterion is the weight-efficiency ratio, (CDS)o/Wp. which shows how much parachute drag area, (CDS)o, is produced per pound of parachute or parachute assembly weight, Wp. Where the cost of the parachute system may be higher than the cost of the payload (such as food or other low dollar-per-pound items), the deciding factor may be cost efficiency, (CDS)0 /$.
Low opening shock is a valid selection criterion for unreefed parachutes, but loses its significance for large, reefed parachutes where reefing controls the force-time history of the parachute opening process.
Growth potential is important in design. Most air vehicles that are recovered by parachute grow in weight during the development cycle because of design changes; changes in requirements: or, when in service, added payloads. An undamaged landing requires maintaining the rate of descent. This may mean increasing the size of the final descent parachute(s) with the concurrent increase in weight and volume of the parachute assembly. The parachute compartment size normally is fixed early in the design cycle of the vehicle and cannot be enlarged. The use of low-pressure packing at the start of the design for the parachute assembly allows storage of a larger parachute assembly later when higher-pressure packing can be incorporated. The use of high-pressure packing at the outset eliminates this possibility.
Repeatability of parachute performance is important for aircraft landing deceleration parachutes that are used 25 to 50 times. Repeatability is also a requirement for ordnance parachutes; parachutes manufactured to the same drawing must provide the same ballistic trajectory.
Table 2-1 is a guide for rating performance characteristics for different applications. Each application and each designer may use different rating values based on the special requirements of the particular application.
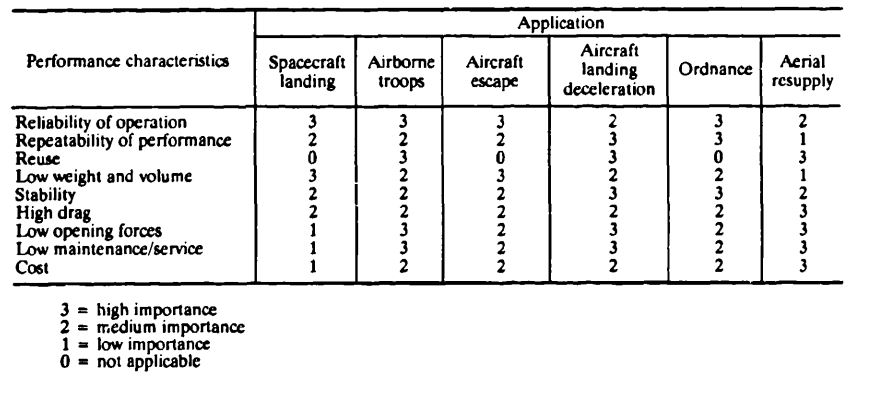
2.5 REFERENCE MATERIAL
The following reports and lecture and symposia papers and proceedings provide information on the analysis, design, testing, and use of parachute recovery systems.
Several parachute handbooks (References 2.1 through 2.4) have been published by the U.S. Air Force. Reference 2.1 covers developments after 1970, and References 2.2 through 2.4 cover the 1950 to 1970 developments.
The Aerodynamic Decelerator Systems Committee of the American Institute of Aeronautics and Astronautics (AIAA) conducts technical symposia. Papers presented at these symposia (References 2.5 through 2.15) are available as conference proceedings or as individual papers from AIAA headquarters in Washington, D.C.
Technical conferences of the Survival and Flight Equipment Organization (SAFE) are listed in Reference 2.16. These conferences cover the entire field of aircrew life-support equipment and aircrew escape.
The University of Minnesota conducts extension courses in aerodynamic decelerator systems technology. References 2.17 to 2.20 list the most recent lectures. Proceedings of these lectures are available from the Aerospace Department of the University of Minnesota in Minneapolis, Minn.
2.5.1 U.S. Air Force Reports
The following unclassified publications are recommended for individuals who want to obtain a general knowledge of parachutes and parachute recovery system application, performance, design, and components.
2.1 U.S. Air Force. Recovery Systems Design Guide, by H. W Bixby, E. G. Ewing, and T W, Knacke. USAF, December 1978. (USAF Report AFFDL-TR-78-151.) Available from the National Technical Information Service, Springfield, Va. 22161.
2.2 _____. Performance of and Design Criteria for Deployable Aerodynamic Decelerators. USAF, December 1963. (USAF Report ASD-TR-61-579.) Available from the Defense Technical Information Center, Cameron Station, Alexandria, Va. 22314.
2.3 _____. USAF Parachute Handbook, Second Edition. WADC Technical Report 55-265, ASTIA Document AD 118036, December 1956.
2.4 _____. USAF Parachute Handbook, ATI No. 35532, March 1951.
2.5.2 AIAA Papers
Proceedings and papers of AIAA conferences on aerodynamic decelerators and balloon technology are listed below.
2.5 Technical papers of the AIAA 10th Aerodynamic Decelerator Systems Technology Conference, Cocoa Beach, Florida, April 1989. Conference proceedings and individual papers are available from the American Institute of Aeronautics and Astronautics (AIAA), 370 L'Enfant Promenade, SW, Washington, DC 20024.
2.6 Various technical papers of the AIAA 9th Aerodynamic Decelerator and Balloon Technology Conference, Albuquerque, N. Mex., October 1986.
2.7 Proceedings of the 8th Conference, Hyannis, Mass., April 1984; available in report form from AIAA.
2.8 Papers of the 7th Conference, San Diego, Calif., October 1981; available as individual paper reprints from AIAA.
2.9 Papers of the 6th Conference, Houston, Tex., March 1979; available in report form from ALAA.
2.10 Papers of the 5th Conference, Albuquerque, N. Mex., October 1976; available as individual paper reprints from AIAA.
2.11 Papers of the 4th Conference, Palm Springs, Calif., May 1973; available as individual paper reprints from AIAA.
2.12 Papers of the 3rd Conference, Dayton, Ohio, September 1970; available as individual paper reprints from AIAA.
2.13 Papers of the 2nd Conference, El Centro, Calif., September 1968; available as USAF Report FTC-TR-69-11, Volumes I and II, from the Defense Technical Information Center, Cameron Station, Alexandria, Va. 22314.
2.14 Proceedings of the ATAA Aerodynamics Deceleration Systems Conference, Houston. Texas; September 1968, available in report form from AIAA.
2.15 Proceedings of the Symposium on Parachute Technology and Evaluation, El Centro, California, September 1964; available as USAF Report FTC-TR-64-12 from the Defense Technical Information Center, Cameron Station, Alexandria, Va. 22314
2.5.3 SAFE Symposia
2.16 Proceedings of the annual SAFE Symposia, covering all aspects of aircrew and cockpit bioengineering, aircrew escape, survival, and rescue. Yearly proceedings are available from the SAFE office, 15723 Van Owen St., Box 246, Van Nuys. Calif. 91406.
2.5.4 University of Minnesota Extension Courses
2.17 Lectures of the 1982 H. G. Heinrich Short Course on Parachute Systems Technology, University of Minnesota, Department of Aerospace Engineering, 110 Union St., S.E. Minneapolis, Minn. 55455.
2.18 Lectures of the 1985 H. G. Heinrich Short Course on Decelerator Systems Engineering, July 1985, University of Minnesota, Department of Aerospace Engineering, 110 Union St., S.E. Minneapolis, Minn. 55455.
2.19 Proceedings of the University of Minnesota/Carl Cranz Gesellschaft Course on Parachute Systems Technology, Fundamentals, Concepts, and Applications; Munich-Oberpfaffenhofen, June 1987. Available from the University of Minnesota, Department of Aerospace Engineering, 110 Union St., S.E. Minneapolis, Minn. 55455.
2.20 Lectures of the 1990 Short Course on Parachute Systems Engineering, May 1990, Boston, Massachusetts. Proceedings are available from the Department of Aerospace Engineering, University of Minnesota, Minneapolis, Minn. 55455.
2.5.5 Miscellaneous References
2.21 Proceedings of the 1986 and 1988 Parachute Manufacturing Seminars conducted by the Piedmont Community College, P 0. Box 1197, Roxboro, N.C. 27573.
2.22 D. Poynter, The Parachute Manual, published by Para-Publishing, P. 0. Box 4232, Santa Barbara, Calif. 91340-4232.